W. Edwards Deming, Out of the Crisis (1982)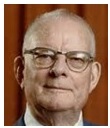
Deming (pictured right) taught the Japanese about quality improvement in the 1950’s. He died in 1993.
He was the most influential thinker in total quality
management.
See also...
W. Edwards Deming in the Management Gurus
section.
Book summary
14 points for quality, competitiveness and
innovation
1. Customer driven purpose
Constantly striving to satisfy present and future customers’ needs through: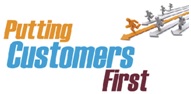
Quality is customer satisfaction.
2. People philosophy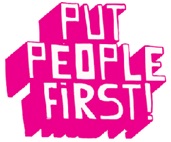
The organization must value its employees and their:
- contribution to quality improvement.
- need for job satisfaction and employment security.
“No one should lose his job for contributing to quality and productivity”, says Deming.
3. Production process
- replace inspection and supervision by incorporating quality into the production
process.
- make self-managing, multi-functional teams of 5-15 employees
responsible for quality improvement
These teams are “QC [quality control] circles” (now known as
quality circles).
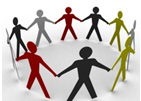
4. Teamwork
Break down barriers between departments, so that people can work in quality control circles (see point 3).
5. Cost minimization (with quality suppliers)
- create a long term relationship with a single supplier for any one item.
- don’t buy from a supplier on price alone.

6. Continuous improvement
Constantly improve quality, productivity and the production or customer service system.
7. Training
Encourage training on the job.
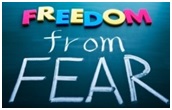
8. Drive out fear
(in the hearts of employees)
9. Eliminate slogans, exhortations and employee targets (like zero
defects)
(because most causes of poor quality are not in employees’ control but in the production system).
10. Avoid numerical goals for managers and employees
Replace them with effective leadership.
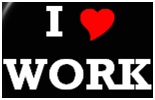
11. Pride of workmanship
Emphasize the quality and fulfilment of work.
12. Education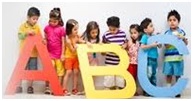
Vigorously support education - for example in
- statistical quality control methods.
13. Quality is everybody’s job
Every employee must work to achieve it, not just the quality control department.
The Shewhart (now sometimes called Deming) cycle is useful here:
14. Leadership
Leaders should give their long term commitment to quality and enable people to find quality improvement
themselves through: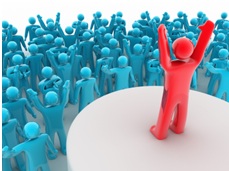
- making sure employees' work is satisfying and well understood (so
that they “do a better job with less effort”).
- removing the causes of failure.
- ensuring consistency of performance.
- asking the right questions and patiently finding the right
answers.
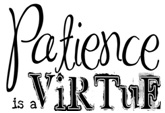
Patience is required...
Because the 14 points will take at least 10 years to implement successfully.
Key quotes on quality
Inspection to improve quality is too late, ineffective, costly...Quality comes not from inspection, but from
improvement in the production process.
Quality control is an obsession.
Key quotes on customers
The customer is the most important part of the production line.
Profit comes from repeat customers – those that boast about the product or service.
Key quote on management
The job of management is not supervision, but leadership.
|