Philip Crosby (1926-2001)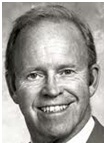
American quality expert whose book Quality Is Free (see below) gave him global acclaim
(pictured right).
Key book
Quality Is Free
(1979)
Quality must become a way of life, being an integral part of an organization's corporate culture.
This requires accepting the five “absolutes” of quality management:
1. Quality means conformance to requirements.
2. Responsibility for quality must be shared by everyone from the top down, not just
by quality control specialists.
3. Quality is achieved through prevention of problems (not inspection) and doing it
right first time.
4. The only quality standard is zero defects.
5. Quality is measured by the cost of doing things wrong
“Quality is free”, because the costs of poor quality (defects, customer complaints, inspection, extra
after-sales service etc) are very high (at least a quarter of sales revenue).
There are 14 steps in the quality improvement process:
- Management commitment (managers should listen, learn, communicate, create solutions to quality problems,
trust people and involve them in quality improvement).
- Quality improvement team.
- Evaluating the cost of quality.
- Establish a committee for zero defects planning.
- Zero defects day (celebrating its achievement).
- Goal setting (challenging quality objectives are vital, particularly zero defects).
- Recognition (with rewards for outstanding performance) .
- Quality councils (voluntary bodies to co-ordinate quality strategy).
Key quotes on
quality
Quality comes from prevention, not detection.
Quality is free. But it is not a gift.
The quality process goes on forever.
Measurement is very important. People like to see results.
Getting people to do better all the worthwhile things that they ought to be doing anyway (how to
make quality certain)
|